We like the idea of collaborative automation. Making automation easier for first time users, the plug and play approach for accessories such as End of Arm Tools, and taking advantage of bringing humans and automated technologies together makes a lot of common sense.
Except when it doesn’t.
Here are some of the reasons why industrial robots make so much more sense when you are considering investing in a robot for your palletizing application:
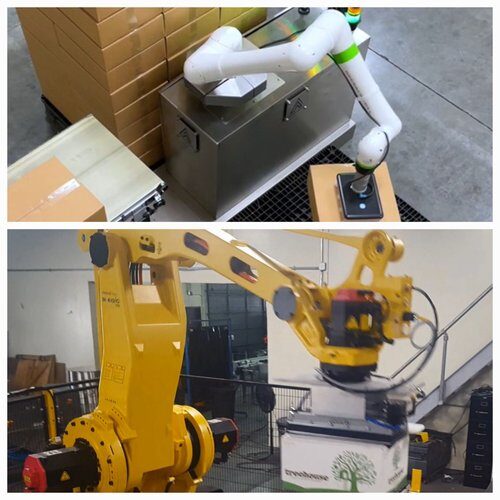
Speed
Collaborative automation works because it is slow, in the collaborative world; slow equals safe. In the industrial world of packaging and automation, slow is expensive. Speed and cycle time is important to manufacturing, for your customers, your business ROI and your stakeholders. Furthermore, cobots in palletizing applications must slow down to a very slow speed (teach pendant speed/ 250 mm per second) once the EOAT/payload reaches above waist height of a person. Why? Because the robot ‘could’ drop the payload, potentially causing an injury. Therefore, the middle and top layers will be palletized much slower than the lower layers. This will dramatically impact throughput productivity.
Robustness
Cobots are light weight— they must be. The internal force sensors are very sensitive, and must be ‘tuned’ to a very light payload to function. Additionally, light weight results in the ability to move the robot a bit faster, as impact is reduced. This coincides with factor #1, speed.
Safety
Safety is important in manufacturing. Safety gates, light curtains, and safety interlocks have been used in industrial settings for decades. They work and they work well. End users just don’t need another layer of safety at the robot.
Cost
There is a misconception that collaborative robots in palletizing applications are cheaper. Many times they simply are not. You need to compare apples to apples including the trade-offs and opportunity costs you may lose by using a less-than-robust robot solution.
Reach
Industrial robots are often larger than cobots because often they need to be able to reach multiple pallet locations, for example. While you might be able to use a traditional FANUC robot and attach AI and advanced sensing to make this a collaborative application, why not just install guarding to keep people out and keep them safe?
Payload
Collaborative robots, in general have limited payload. This is inherent to the design: speed limited, limited acceleration and payload limited, it’s part of what makes a cobot a cobot. Payload is important when it comes to robots and that is why we spend a lot of time engineering such as calculating the mass of the case, the EOAT, PLC code, inertia and reach required.
End of Arm Tooling
The end of Arm Tools for industrial palletizing robots need to be able to handle larger payloads because they may require a larger end of arm tool, and the increased mass of an EOAT with the part in the gripper cannot be underestimated. Underpowering a robot is a common error in industrial automation and happens far too often when trying to use a cobot for palletzing.
Total Cost of Ownership
The promise of a cheaper solution in the automation industry is usually about moving or downloading engineering costs around or to the end user. Cobot palletizers may save you about 20% to 25% of a $125K to $150K robotic palletizer. Considering the design life of an industrial robot at 20 years, amortizing this small amount is not a considerable advantage.
Will the lightweight cobot last 20 years?
And with how many repairs?
Maintenance, even electrical power draw is very similar cost from cobots to industrial robotics.Cobots do not offer an advantage here.
An automation Distributor is not an Automation Integrator
One of the new models to distribute collaborative robots is via a distributor. These are people and companies that sell technical equipment: servo motors, PLC, sensors, etc. They are not really used to packaging up a total solution and if they are, they are likely not used to the service and support model that many manufacturers require.
The Value of Using a Robot Integrator
One of the big values to using an integrator is experience. That is one of the things that you are buying when you engage with an experienced automation integrator. Integrators have seen thousands of applications, built hundreds robot toolings, know the difference between accessories such as sensors, dress packs and conveyors. An automation integrator conducts a professional risk assessment study to assure the robot meets OSHA and RIA guidelines for human safety requirements. An automation integrator takes full turnkey responsibility – there is no pointing fingers when you are working with an integrator. Automation Integrators employ technical expertise including applications engineers, electrical and mechanical designers, PLC programmers, toolmakers, technical integrators and service and support people.
Automation is not a DIY experiment. Or Automation Shouldn’t be Do it Yourself
When you are thinking of Robot Palletizers for your manufacturing operation and are seeing ads and promotions about DIY “standard products” to solve your material handling needs, contact us. We won’t make you create your own robot reach study or be responsible for your own pallet reach study. You won’t be alone in choosing an end effector or end of arm tool.
We do this engineering for you
We are happy to have a frank conversation about when an off-the-shelf solutions are best and very simple and where custom palletizers using industrial robots may be a better long term fit for your business.
Call our Applications Engineering Department at 714.881.4988 or email us at info@transautotech.com
OUR PARTNERS
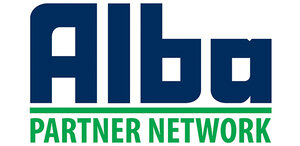
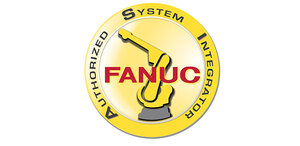
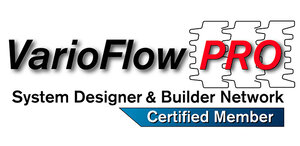
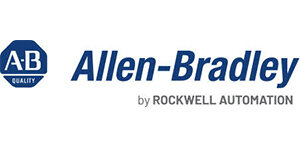
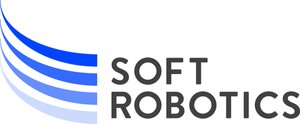
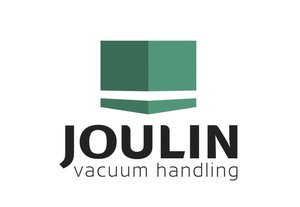

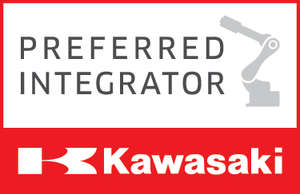