Robots are very flexible, relatively inexpensive, highly reliable and can be reprogrammed quickly. Robots can palletize multiple production lines simultaneously. This allows you to respond as your business grows or your customer requirements change.
Yes, this can be done by the end user or we can do it for you. There are certain changes such as zone guards, escapement devices, end of arm tools where you may need our assistance but we find often our customers can make the changes themselves. Either way we’re happy to help!
Robots are typically very low maintenance but it can depend on the environment. If the environment is hot or dusty, there may be a need for robot accessories like coverings and additional fans. Many robots can run 10 years with little maintenance other than lubrication, cleaning filters and visual inspections for wear parts.
With many of our systems, you don’t need robot programmers or maintenance people on site. Our systems are supplied with a robust operating system with good, generic error messaging and documented procedures for error recovery, startup and shut- downs.
Yes, we do offer preventative maintenance and can schedule this out monthly, quarterly and annually depending on your needs, facility shutdowns, etc.
All of our end of arm tools (EOATs) are supplied, customized or built by TransAutomation for each application from boxes to bags of powder bulk or solids.
Our warranty is normally 1 year on supplied parts and third party supplied items, such as conveyors, robots and control devices.
With each system we supply a list of our recommended spare parts, wear parts and emergency parts. We suggest the parts based on our extensive experience in the industry and availability of components locally. Examples of spare parts can be sensors, fuses, batteries, and filters.
Likely the answer to this is no, unless you are in a rare situation. If the tool is designed correctly, the subcomponents should be easily replaceable. The last thing we recommend is to have replacement tools on your shelf for years.
This happens from time to time. In this case we would come to your facility, review your requirements and material flow and look to see if you can add automation, change robots, or add conveyors to decrease cycle time and address capacity challenges.
Yes, we can absolutely come in and train or retrain your staff at your convenience. We can even package this up with a preventive maintenance package.
Yes we offer remote support. We like remote support as it saves travel time and reduces cost. With your permission, we can dial into each system via a VPN connection to debug and provide support to keep your robot, automation and palletizers up and running and secure.
OUR PARTNERS
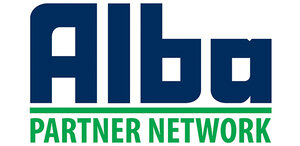
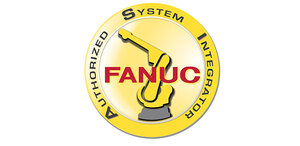
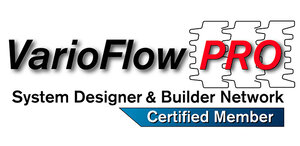
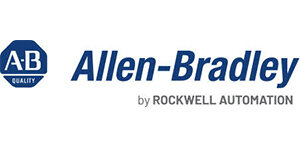
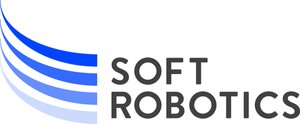
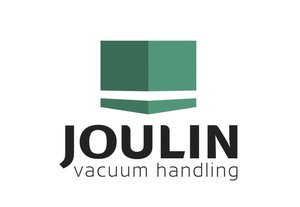

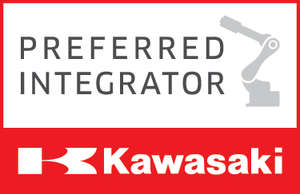