Case Study
Manually stacking heavy bags is a dull, dirty and dangerous job.
The proof of this was evidenced every day at Frank Pellets manufacturing facility in Mill City Oregon.
Frank Pellets manufactures compressed wood fuel pellets that are packaged in large bags weighing up to 50 lbs. Every shift would require up to 3 employees to spend the entire day doing the backbreaking work of stacking the bags onto pallets at the end of the production line. The heavy bags are capable of coming out of the filling machines at a rate of 10 bags per minute, a challenging rate for workers to maintain. Keeping staff to perform this job for even one shift was becoming difficult.
Seeking to improve production speeds, reduce manual labor and improve employee productivity, Frank Lumber sought a robotic solution to improve their operation.
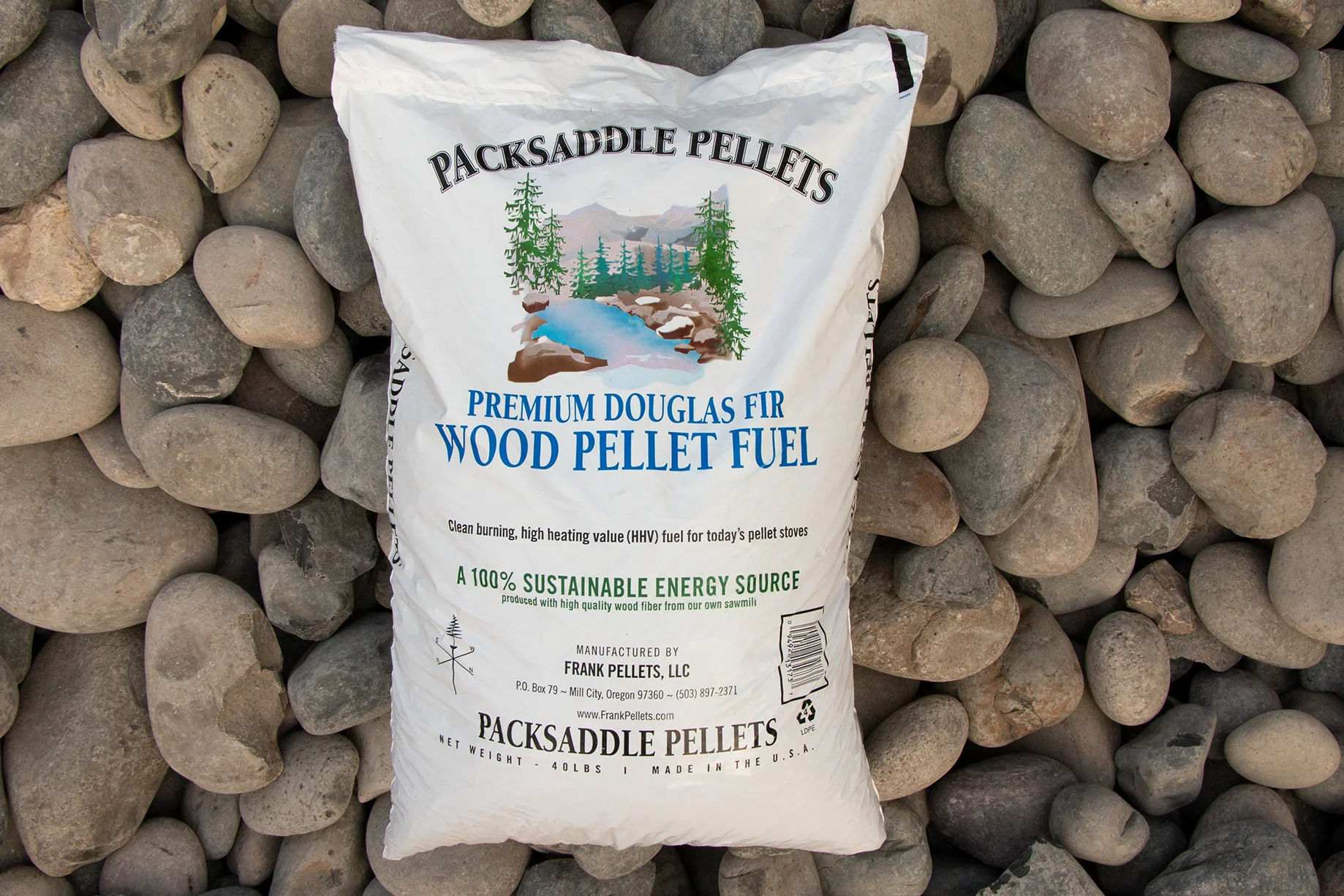
Challenges
- Increase production speeds to 10 BPM
- Reduce manual labor
- Improve employee safety and productivity
Results
- Increased production speeds to 10 BPM
- No manual labor required for stacking
- Manual labor utilized in other production areas
Story
Manually stacking heavy bags is a dull, dirty and dangerous job. The proof of this was evidenced every day at Frank Pellets manufacturing facility in Mill City Oregon. That is, until a robot arrived on the scene and changed everything.
Frank Pellets, a subsidiary of Frank Lumber, manufactures compressed wood fuel pellets that are packaged in large bags weighing up to 50 lbs. Every shift would require up to 3 employees to spend the entire day doing the backbreaking work of stacking the bags onto pallets at the end of the production line. The heavy bags come out of the filling machines at a rate of 10 bags per minute, a challenging rate for workers to maintain.
This wood pellet production line runs 8 hour shifts (three shifts in peak season). Keeping staff to perform this job for even one shift was becoming difficult.
Fuel pellet manufacturing is a growing industry in North America. Wood pellet fuel is a clean-burning biomass product made of renewable substances. Pellets are a cost-stable home heating alternative currently used in approximately 1,000,000 North American homes.
Frank Pellets knew that the demand for labor was not about to stop, or even slow down.
Established in 2008 to utilize the wood waste steam from their adjacent milling operation, Frank Pellets manufactures compressed fuel pellets which are filled into 33- pound and 50-pound bags, and ships to customers throughout the Pacific Northwest.
Seeking to improve production output, as well as reduce employee injury risk, Frank Pellets sought a robotic solution to improve their operation.
To achieve an automation solution, Frank Pellet partnered with FANUC Authorized System Integrator Trans Automation Technologies Inc. in Irvine, CA. FANUC Robotics offers a full line of heavy-duty, multiple axis industrial robots. Trans Automation Technologies offers extensive experience in the design and production of custom robotic palletizing systems. Among these include palletizers for heavy bagged products. For the Frank application, a FANUC model M410-185 robot was selected for its heavy payload and speed capacity.
Palletizing bags is challenging due the inherent characteristics of the product. Filled bags may change shape due shifting contents or may require conditioning prior to pick up by the robotic end of arm tool.
The Frank Pellets robotic palletizing system includes an automatic pallet dispenser with pallet conveyor to deliver pallets to the robotic load position. In addition, a slip sheet applicator places corrugated sheets onto the pallet prior to loading.
The primary component of the robotic palletizer is the FANUC M410-185iC 4-axis robot, with a 185 kilogram (408 pound) payload. The robot employees a HVLP (high volume low pressure) vacuum gripper tool on the end of the robot’s arm. The tool has a large oval vacuum port with a rubber foam seal on its perimeter. Via the FANUC M410 robot’s wrist, the high-volume vacuum gripper is pressed onto the bags flat surface, and the vacuum seal is made. The bag is positively attached to the robot’s gripper with vacuum, transported to the correct position on the pallet and is released with a reverse vacuum ‘blow-off”.
Full pallets of the wood pellet bags are discharged from the robot cell to be removed from the system by forklift. The system begins stacking a new pallet automatically without any attention from workers.
A full-perimeter safety barrier with electronic interlocks provides safety for employees from the fast-moving machine.
The new FANUC robotic palletizer is capable of operating 24-hours per day stacking bags at the required rate of 10 bags per minute. Without the need for manual bag stackers, this system provides a very attractive ROI and risk of injury avoidance for Frank Pellets.
The robotic palletizer works better than we anticipated.
It has sped up our production process, freed up three employees to do other tasks, while the robot is doing the hard work.
We are very happy with the outcome.
We should have purchased this robotic palletizer a long time ago – it is the best investment we have made so far regarding the wood pellet Industry.
John Griesenauer, Plant Manager
Frank Pellets
Technologies
- Robotic Palletizer
- Pallet Handling Conveyor
- High volume low pressure gripper
Partners
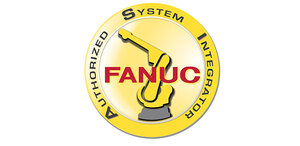