Robots can often be utilized for case packing applications, in addition to robotic palletizing, due to the benefits to floor space usage and variability that robot system can offer.
Robots can perform high speed repetitive tasks without taking a break or risk of physical injury. Implementing a robot in your case packing process can be a solution for bagged products, bottles, cartons, cans, and sleeved or shrink-wrapped items. Robotic case packing systems are customized according to customer’s products.
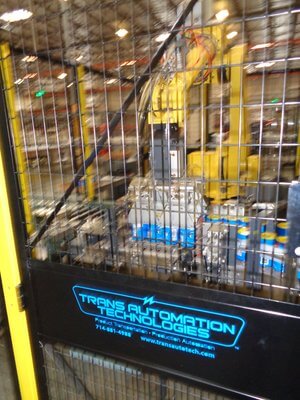
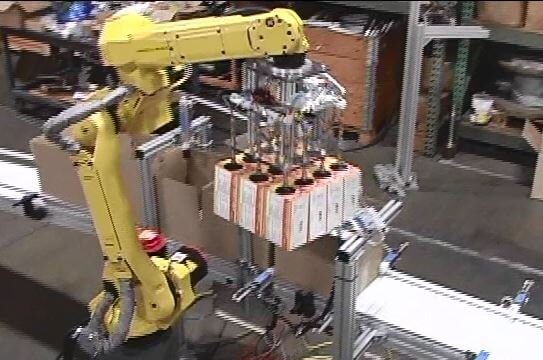
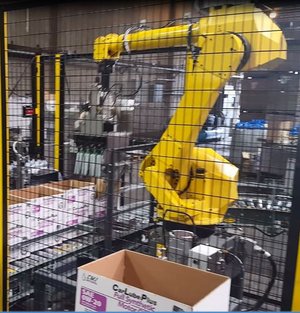
While drop packers are often the ‘go-to” method of getting bottles into a case, some products do not lend themselves to drop packing. Glass bottles often cannot take the impact of drop packing.
Case pack patterns that do not allow standard in-line geometric arrangements of product, such as dual shrink-wrapped stacks of cans, which requires rotation of the product bundle to meet the case pack patterns, can be case packed with robots, due the end effectors rotational capability.
Robots can perform virtually any motion within the case packing envelope, whereas drop packers must be linear.
In slower applications where demand allows, robots with adequate reach can serve two or more products on two or more lines, alternating between the 2 lines, where typically such an application would require two drop packers.
When floor space is a concern, a robotic case packer can present a much smaller than a drop packer.
Some of the more challenging and cost-adding aspects of a robotic case packing system can often be the staging the product and the cases, rather than the robotic pick and placement itself.
For example, in our 12 x 1 quart motor oil case packing robot system we completed, a 4 x 3 matrix must be formed for the robot to pick the proper case load pattern.
In this instance, filled bottles which are processed in a single file product is must first be diverted into 4 lanes, and then 3 rows must be “isolated” from the back pressure of subsequent bottles during the robots pick cycle. This is done using custom conveyors and a linear actuator lane divider to cause the flow of bottles into 3 lanes, then using pneumatic devices to release back-pressure on the first 4 products in each lane. The robot end effector, with a 12 suctions cups in a 4 x 3 pattern, picks up the entire caseload and places it in the case.
Also, case positioning, flap control and speed of case exchange are important factors to complete correctly in a robotic case packer operation. This is where the highly accurate world of robotic meets the not-so accurate world of corrugated cardboard. Case can be deformed out of shape, cause the robot’s payload to hit the case side. The shipper case’s major or minor flaps must be controlled to keep them from folding over into the carton and creating an obstruction for the robot. Properly cycling fresh, empty case into the robot, and rapidly transporting full case away from the robot are crucial to making high cycle times.
A high-speed, compact robotic case packing system is very helpful in reducing floor space usage, reducing labor and improving productivity. Robotic case packers are suitable for applications in industries such as consumable products in bottles, cartons, bags, food, tea, chemical, electronic products, E-commerce, etc.